Adsorption dehydration units can reduce the water content of a gas stream to less than 0.1 ppmv. The gas industry normally uses adsorption dehydration units upstream of a liquefied natural gas (LNG) plant or a deep natural gas liquid (NGL) extraction plant where the gas temperature reduces to less than -160 °C (-256 °F) and -100 °C (-148 °F), respectively. Removal of water content to this very low level is essential to prevent freezing. One can find the details of the adsorption dehydration process and the descriptions of equipment in Chapter 18 of John M. Campbell textbook [1].
The PetroSkills’ May 2015 tip of the month (TOTM) [2] discussed the efficient operation of molecular sieve dehydration units. Specifically, it discussed the benefits of standby time in the adsorption dehydration processes.
This month’s TOTM discusses feed gas flow rate, pressure, and temperature effect(s) on the followings:
- Mass of Desiccant
- Bed Diameter
- Bed Height
- Regeneration Gas Rate
- Regeneration Heating Load
- Regeneration Cooling Load
- Regeneration Gas Heater Load
This discussion spans gas volume rates from 2.83×106 to 11.32×106 Sm3/d (100 to 400 MMSCFD. It examines this range at two temperatures: 30°C (86°F) and 40°C (104°F) with each temperature evaluated at two adsorption pressures: 6.207 MPaa (900 psia) and 8.0 MPaa (1160 psia).
Figure 1 shows a simplified process flow diagram for a 3-tower system [1]. In this TOTM, the specified parameters are:
- Desiccant = Molecular Sieve Type 4A, 3.2 mm (1/8 in) diameter
- No of towers = 3
- No of towers on-stream = 2
- Adsorption time = 16 hours
- Step time (same as total regeneration time) = 8 hours
- Stand-by time = 0 hours
- Equalization time = 0.5 hours
- Heating time = 4.88 hours
- Cooling time = 2.62 hours
- Desiccant loading capacity, ΔXnew = 19 wt% (mass of water/100 mass of desiccant)
- Desiccant life factor FL = 0.6 (Based on 3 years and average performance)
- Desiccant relative density = 0.705
- Desiccant heat capacity = 1.0 kJ/kg-°C (0.24 Btu/lbm-°F)
- Steel heat capacity = 0.5 kJ/kg-°C (0.12 Btu/lbm-°F)
![Figure 1. A simplified process flow diagram for a 3-tower adsorption dehydration system [1].](http://www.jmcampbell.com/tip-of-the-month/wp-content/uploads/2015/09/fig1.png)
Figure 1. A simplified process flow diagram for a 3-tower adsorption dehydration system [1].
Based on the procedure and steps of Chapter 18 [1], this TOTM utilized a revised version of PetroSkills/Campbell GCAP software [3] to perform all of the calculations.
Figure 2 shows variation of the required mass of desiccant with the feed gas rate, pressure and temperature. As the water load increases, the required mass of desiccant increases for a constant adsorption time. Note that the feed water load increases with increase in feed gas rate and temperature and decrease in pressure. The feed with higher temperature and lower pressure requires more mass of desiccant. For the same reason, the feed with lower temperature and higher pressure requires less mass of desiccant.
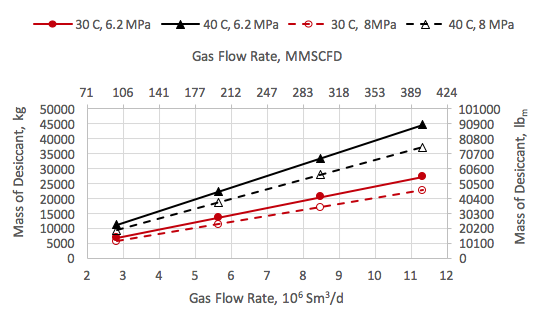
Figure 2. Variation of mass of desiccant with the feed gas rate, pressure and temperature.
The mass of the desiccant in the tower and pressure drop criteria establish the tower diameter and height of desiccant. This is a trial and error calculation. Figure 3 shows variation of the minimum bed diameter with the feed gas rate, pressure and temperature. This figure indicates that feed with higher water load (higher temperature and lower pressure) needs a bed with larger diameter and feed with lower water load (lower temperature and higher pressure) requires a smaller diameter.
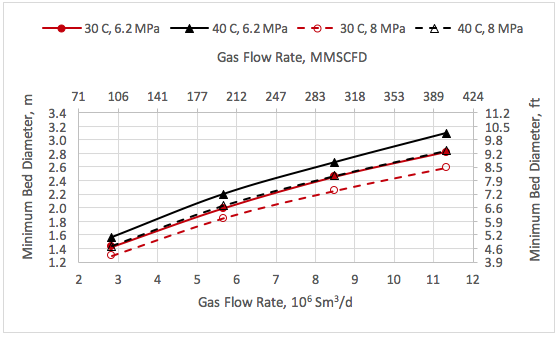
Figure 3. Variation of bed diameter with the feed gas rate, pressure and temperature.
One can calculate the desiccant height from the mass of desiccant, bed diameter, and desiccant density. Figure 4 shows the variation of the minimum desiccant height with the feed gas rate, pressure and temperature. Similarly, this figure indicates that feed with higher water load (higher temperature and lower pressure) requires a taller beds and feed with lower water load (lower temperature and higher pressure) requires shorter bed heights.
For all cases, the lean and dry regeneration gas had a relative density of 0.59 and pressure of 2.069 MPaa (300 psia) but its temperature was the same as the feed gas temperature. Its temperature from heater was 532.2 °C (550 °F) and the final bed regeneration temperature prior to cooling was 288 °C (500 °F).
Figure 5 shows the variation of the regeneration gas requirement with the feed gas rate, pressure and temperature while maintaining constant heating and cooling times. This figure indicates that higher water loads require more regeneration gas. Similarly, Figures 6, 7, and 8 show the variation of the required heating load, cooling load, and regeneration gas heater load, respectively, with the feed gas rate, pressure and temperature.
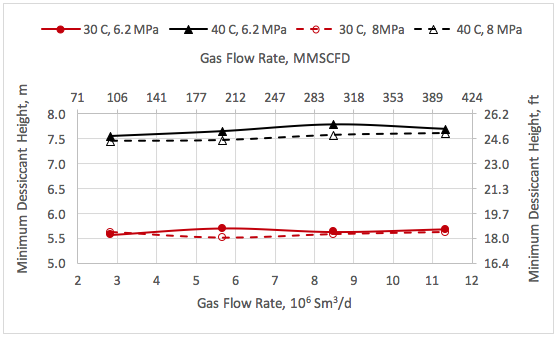
Figure 4. Variation of desiccant height with the feed gas rate, pressure and temperature.
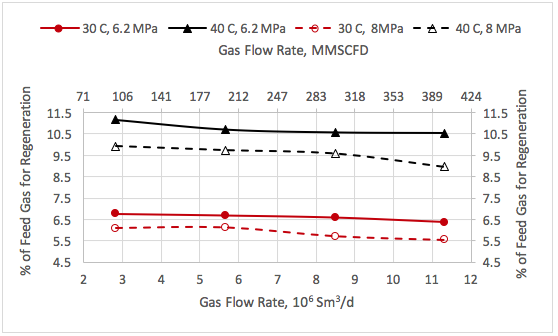
Figure 5. Variation of % feed gas for regeneration with the feed gas rate, pressure and temperature.
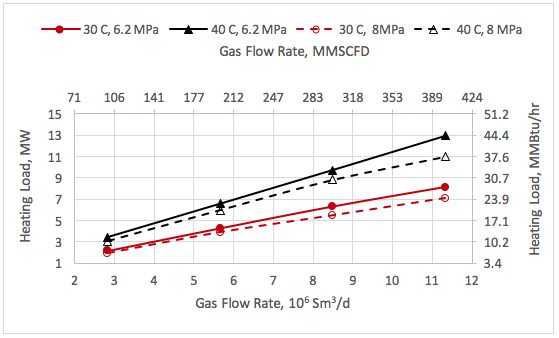
Figure 6. Variation of heating load with the feed gas rate, pressure and temperature.
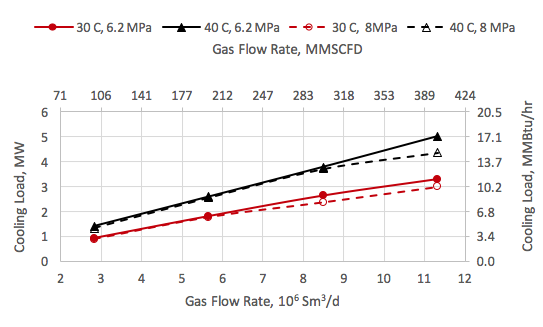
Figure 7. Variation of cooling load with the feed gas rate, pressure and temperature.
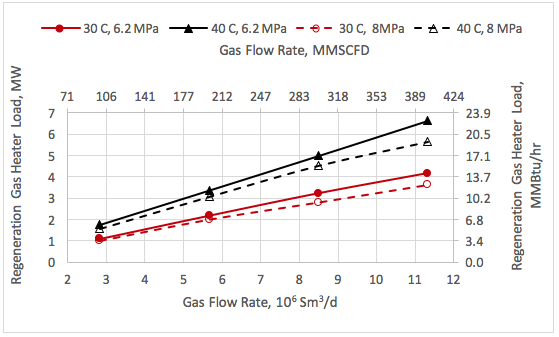
Figure 8. Variation of gas heater load with the feed gas rate, pressure and temperature.
Summary:
Water content of the feed gas affected by temperature, pressure and flow rate is the key factor in sizing and operation of adsorption dehydration system. Higher water load requires a larger size bed, higher heating and cooling loads and higher rate of regeneration gas.
To learn more about similar cases and how to minimize operational problems, we suggest attending our PF49 (Troubleshooting Oil and Gas Facilities), PF42 (Separation Equipment Selection and Sizing), G4 (Gas Conditioning and Processing), G5 (Gas Conditioning and Processing – Special), and PF4 (Oil Production and Processing Facilities), courses.
PetroSkills offers consulting expertise on this subject and many others. For more information about these services, visit our website at http://petroskills.com/consulting, or email us at consulting@PetroSkills.com.
Dr. Mahmood Moshfeghian
References:
- Campbell, J.M., Gas Conditioning and Processing, Volume 2: The Equipment Modules, 9th Edition, 2nd Printing, Editors Hubbard, R. and Snow–McGregor, K., Campbell Petroleum Series, Norman, Oklahoma, 2014.
- Malino, H. M., http://www.jmcampbell.com/tip-of-the-month/2015/05/benefits-of-standby-time-in-adsorption-dehydration-process/
- GCAP Version 9.1.1, Gas Conditioning and Processing Software, Editor Moshfeghian, M., PetroSkills/Campbell, Norman, Oklahoma, 2015.
Please include myself for the tip of the month article. Thanks.
Please dd for the tip of the month article.
Thanks.
[…] PetroSkills’ May 2015 [2] and October 2015 tip of the month (TOTM) [3] discussed the efficient operation of molecular […]
graet
great