In the post-World war II period, the steels used in the oil and gas industry were quite different from what we use today. This tip of the month (TOTM) presents a brief overview of improvements in the steels used in oil and gas processing equipment for safer and more reliable operations.
Plate was SA-285C a 55,000 psi (379 MPa) tensile steel that was relatively soft and easy to fabricate. It was not killed steel and therefore, not fine grain steel. The low tensile strength meant thicker vessels and because of poor welding techniques, spot or no radiography at all was common, making the items even thicker. Figure 1 shows a vacuum tower made of SA-285C from the 1950’s. This tower was constructed in 1961 by Chicago Bridge and Iron for the Shell Martinez Refinery in California.
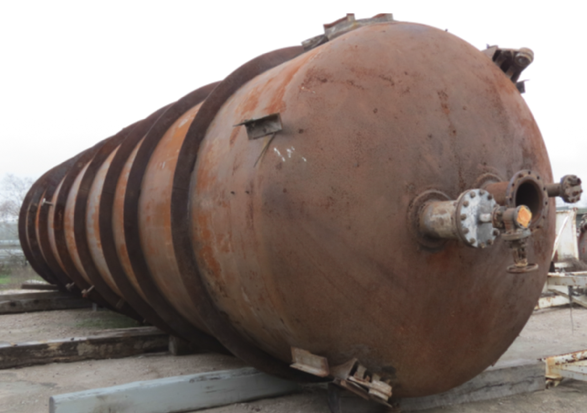
Figure 1. A vacuum tower made of SA-285C from the 1950’s. Shell Martinez serial #C-4201
A plate designated SA-212B Firebox was in use for higher tensile applications. It had a 70,000 psi (482 MPa) tensile, but was coarse grained and had the undesirable characteristic of fracturing in the parent metal after thermal expansion and contraction over a period of time. Due to repeated failures in service, this material was removed from the ASME Boiler and Pressure Vessel Code Section II in 1968 as being unfit for thermal cycling. Figure 2 presents a high pressure molecular sieve tower which was fractured by thermal cycling.
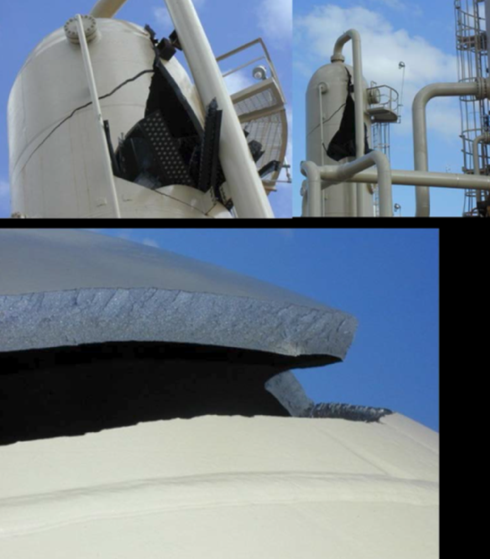
Figure 2. An example of fracturing in a vessel made from the SA-212B Firebox steel.
Pipe used in the 1950’s was SA-53B, which could be Electric Resistance Welded or seamless. It was not killed steel. It had a 60,000 psi (413 MPa) tensile and was the pipe of choice for vessel, tank, and piping fabrication at the time.
The forging of the 1950’s was SA-181, a 60,000 psi (413 MPa) tensile steel used for flanges, forged steel fittings, and heavy nozzles. It was not killed steel.
Since none of these steels were killed, fine grained steels, their use declined rapidly as the industry moved into harsh environments such as the North Slope of Alaska and the processing of acid gases and sour crudes.
Killed steel came into wide use during the 1960’s. Killed steel is produced in the ladle by adding silicon or aluminum to prevent further deoxidation of the heat. Molten steel contains dissolved oxygen which can cause bubbles in the cooling and solidification process. The addition of silicon or aluminum stops the reaction of the oxygen with carbon, producing a fine grain steel free from dissolved gases, highly homogenous with excellent fabrication properties.
During the 1960’s, the SA-516 family of plate steels was introduced. These steels were silicon killed, fine grained, and produced excellent properties. The fine grain gave the steel impact resistance at temperatures down to -50 °F (-45.5 °C). The SA-516 suffix defines the tensile strength, 55,000, 60,000, 65,000, and 70,000 psi (379, 413, 448, and 482 MPa).
- SA-516-55 was designed to replace SA-285C
- SA-516-60 was designed for use in very cold service.
- SA-516-65 was for intermediate tensile requirements
- SA-516-70 was to replace SA-212B Firebox plate
The chemical and mechanical properties of these four grades of steel overlap to the extent that one plate can actually meet all four specifications.
Approximately 90% of all custom carbon steel pressure vessels manufactured for the oil and gas industry in the world today are made from SA-516-70 or its UNS (Unified Numbering System) equivalent. Figure 3 presents an example of a vertical drum made of SA-516-70.
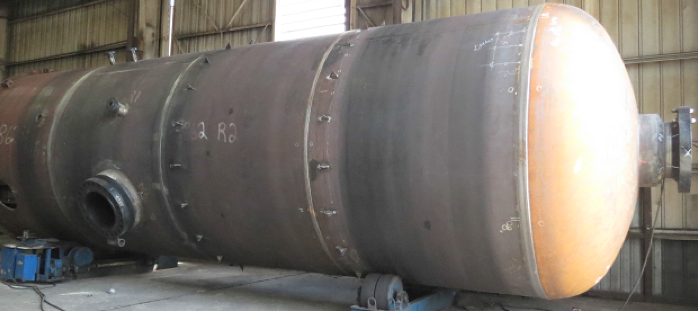
Figure 3. An example of a vertical drum made of SA-516-70
During the 1960’s SA-106 pipe replaced SA-53 as the pipe of choice. Unlike SA-53B, SA-106B is seamless, killed, fine grain steel. It has a 60,000 psi (413 MPa) psi tensile.
In 1978, SA-105 forgings replaced the SA-181 as the forging material of choice. SA-105 has a tensile of 70,000 psi (482 MPa), so the pressure ratings of B16.5 carbon steel flanges increased.
Around the year 2000, the pipe manufactures improved their processes making SA-106 pipe to the point that they are able to meet the chemical and mechanical properties of SA-106B and SA-106C in the same heat.
Since 2003, basically all SA-106 pipe is dual certified to SA-106B and SA-106C. This means that all three major components of a pressure vessel or shell and tube heat exchanger now have the same tensile strength, 70,000 psi (482 MPa). Figure 4 presents pipes made of SA-106.
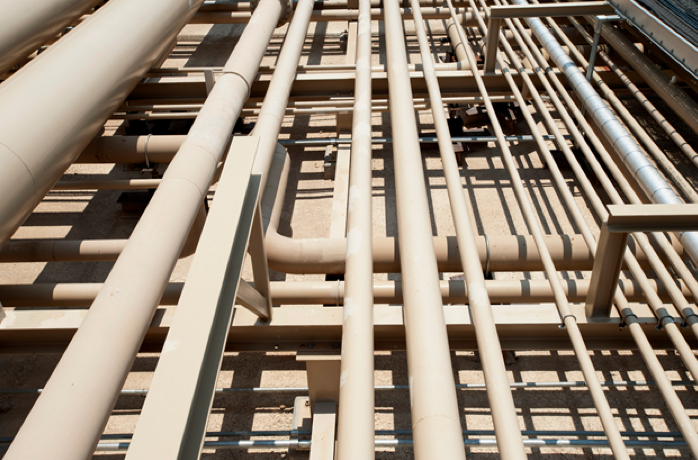
Figure 4. Pipes made of SA-106
Austenitic Stainless steels (300 series) fifty years ago were made to straight grade (0.08 carbon) or “L” grade (0.03 carbon). Steel service centers had to maintain stocks of both grades. About 45 years ago, the stainless mills improved their manufacturing techniques to produce dual certified stainless steel, meaning that virtually all stainless in the steel service centers meets the criteria of 0.03 carbon for “L” grade but also meets the mechanical properties of straight grade. Straight grades have a higher tensile allowing for the use of a thinner plate than “L” grade plate.
Figure 5 presents an example of a separator made of stainless vessel. This 316 stainless separator is the first to be used offshore in place of a clad vessel. Since the temperature was low, the higher tensile allowed this item to be thinner, saving weight, and not require PWHT (Post Weld Heat Treatment), impact testing or special paint.
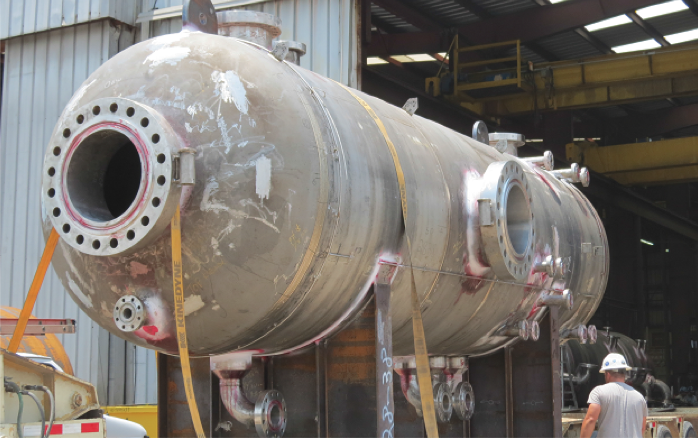
Figure 5. This 316 stainless separator is the first to be used offshore in place of a clad vessel
Summary:
In the last half century, the adoption of new technology in the manufacturing of fine grain steel plates, pipes and forgings has vastly improved the quality of the steels used in Oil and Gas Processing Equipment. Along with improvements in the welding processes used to construct Oil and Gas Processing Equipment, vessels, exchangers, piping and storage tanks are safer than ever before.
To learn more about similar cases and how to minimize operational problems, we suggest attending our ME43 (Mechanical Specification of Pressure Vessels and Heat Exchanges), PF49 (Troubleshooting Oil and Gas Facilities), PF42 (Separation Equipment Selection and Sizing), G4 (Gas Conditioning and Processing), and PF4 (Oil Production and Processing Facilities), courses.
PetroSkills offers consulting expertise on this subject and many others. For more information about these services, visit our website at http://petroskills.com/consulting, or email us at consulting@PetroSkills.com.
John R. Curry
Instructor and Consultant
References:
- ASME Boiler and Pressure Vessel Code Section II, Part A., American Society of Mechanical Engineering, 1968.
iphone5 ブランド スーパーコピー 代引き http://www.brandiwc.com/brand-47-copy-0.html
some really howling work on behalf of the owner of this site, absolutely outstanding articles.
I like this web site because so much utile material on here : D.