La mejor manera de prevenir la formación de hidratos (y corrosión) es la de mantener las líneas de transmisión, tuberías, y equipos libres del agua líquida. Existen ocasiones, malas o buenas, cuando la decisión es tomada para operar una línea o proceso conteniendo agua líquida. Si es ésta la misma, y la temperatura del proceso es menor que la temperatura de hidratación, la inhibición de esta agua puede ser menester. Este fenómeno es de particular importancia en los sistemas de recolección de gas, y las de operaciones bajo el nivel del mar durante la producción normal así como la de cierre de las mismas [1,2].
Muchos materiales pueden ser agregados al agua para lograr reducir tanto la temperatura de hidratación así como la de congelamiento. Por varias razones prácticas, un inhibidor termodinámico tal como el metanol o uno de los glicoles es aplicado, generalmente el monoetilén glicol. Todos pueden ser recuperados y recirculados, pero la economía de la recuperación del metanol puede que no sea favorable en todos los casos. La prevención de los hidratos con el metanol y/o los glicoles puede incurrir en ciertos gastos elevados debido a la dosificación elevada ( entre unos 10 hasta 60 % por peso en la fase acuosa). Elevadas concentraciones de estos solventes agravan a potenciales problemas con las escamas por cuanto se reduce la solubilidad de éstas en el agua y se precipitan la mayoría de los inhibidores de escamas [2]. La inyección total requerida del inhibidor es la cantidad/concentración de éste en la fase líquida del agua logrando la depresión requerida de la temperatura de hidratación, mas la cantidad que también será distribuido en la fase gaseosa y las demás fases de los hidrocarburos. Cualquier inhibidor en la fase gaseosa impacta o la fase líquida de los HC logra poco impacto en la formación de los hidratos.
Pérdidas de solubilidad del MEG en la fase de gas es despreciable así como la fase líquida de los HC. Sin embargo, las pérdidas de metanol son más significativas, particularmente en la fase de vapor. El contenido de metanol de las fases tanto de vapor así con líquido de los HC depende de la temperatura, presión, y composición. Basado el documento “GPA-Midstream RR 149” [3] el contenido de metanol en la fase de gas puede llagar hasta 0.075 mol% (750 ppmv) y en la fase líquida hasta 0.6 mol%. Dependiendo de las pérdidas por solubilidad, la reposición química del metanol pude ser importante así como costoso para tanto los sistemas de flujo directo, así como los de recuperación del methanol.
La cantidad significativa de pérdida de metanol en las fases de los hidrocarburos puede causar problemas en la refinerías, plantas petroquímicas, de GNL, más otras aguas abajo. En las plantas donde es recuperado el propano, el metanol se acoplará al producto de propano y presentará una causa potencial para que éste se desvíe de especificación de venta. Metanol igual se ha visto ser causa de las fallas prematuras en los tamices moleculares. En las refinerías, el metanol debe ser lavado de la corriente crudo/condensado, en donde perfila un problema para el tratamiento del agua de despojo. En las plantas petroquímicas, el metanol también se considera un veneno para algunos lechos catalizadores. El lector puede informarse adicionalmente en la referencia [4].
En el Previo del Mes de Octubre 2010 (PDM) fue considerado la presencia de metanol en la corriente de producción crudo/gas/agua, y fueron determinadas las trazas de metanol resultantes en el gas deshidratado con el TEG [5]. Ese previo estudió el impacto de la temperatura del gas húmedo, el número de platos teóricos en la torre contactora, la especificación para el contenido de agua del gas seco, y el caudal de circulación sobre el nivel de concentración del metanol en el gas seco.
El Previo del Mes de Julio 2010 comparó el rendimiento del monoetanolamina (MEA), dietanolamina (DEA), y el metildietanolamina (MDEA) mediante la simulación de una unidad de endulzamiento [6]. La concentración del H2S y CO2 en el gas dulce, gasto de la solución de amina, carga térmica del re hervidor, pérdidas de aminas, potencia de bombeo, y la carga térmica del intercambiador rico-pobre fueron calculados y graficados par un rango amplio de las tasa de vapor de agua requeridas para la regeneración de la solución de amina rica.
Este Previo del Mes considerará la presencia de Metanol en una corriente de gas agrio y determinará las trazas cuantitativas del mismo que permanecen en el gas dulce, gas de despojo (flash gas), y corrientes de gas ácido. Para lograr esto, el previo simulará por computadora, un esquema simplificado de endulzamiento de un gas.
Igual será analizado el impacto de la temperatura del gas agrio, contenido de metanol, y la tasa a la cual se reemplaza el reflujo condensado con agua fresca sobre el contenido de metanol en el gas dulce. Para las dos temperaturas del gas agrio en 32.2 y 43.3 °C (90 y 110 °F) este previo analiza tres concentraciones de metanol inyectado de 50, 250, y 500 PPMV. En cada caso el previo varía el reemplazo del agua fresca entre 0 y 100 % con incrementos de 20 %. Los resultados de la simulación son presentados en gráficos correspondientes.
Caso en estudio:
Para el propósito de ilustración, este previo considera el endulzamiento de 2.832 x 106 Sm3/d (100 MMpcsd) de un gas natural aplicando el MDEA. La Tabla 1 presenta su composición, presión, y temperatura. El previo aplica el conjunto de programas de simulación en computación (software) ProMax [9] con el “paquete” “Amine Sweetening – PR” aplicado en los cómputos de simulación correspondientes.
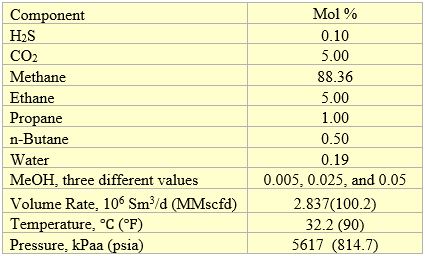
Tabla1. Composicion de la corriente de entrada, su gasto, y otras condiciones
La Figura 1 [9] presenta un proceso de endulzamiento modificado para el caso en estudio. Una fracción importante del metanol entrando con el gas agrio se despoja de la unidad de endulzamiento en las corrientes 4 (Gas Dulce), 6, (Gas de Despojo), y 12 (Gas Acido). Sin embargo, algo del metanol es retenido y acumulado en el sistema y logra su máxima concentración en la corriente 10 (Reflujo). Para lograr reducir adicionalmente ésta concentración en el gas dulce, una fracción de la corriente de reflujo es purgada vía una corriente de “Despojo de Agua” y ésta reemplazada con “Agua Fresca”. La Figura 2 presenta la ampliación de la esquina superior de la derecha de la Figura 1 la cual indica estas corrientes de despojo de agua y agua fresca.
En la Figura 2, la corriente de “Despojo de Agua” elimina una fracción especificada de la corriente 10A (el reflujo condensado), y la corriente de “Agua Fresca” le agrega el mismo caudal al proceso. Para ilustrar el efecto de este reemplazo de agua sobre la reducción del contenido de metanol del gas dulce, la fracción del agua condensada es variada entre 0 y 100% con incrementos de 20 % sobre base molar.
![Figura 1. Un Proceso Simplificado de una unidad de endulzamiento con Amina [9]](http://www.jmcampbell.com/tip-of-the-month/spanish/wp-content/uploads/2016/07/Fig1.png)
Figura 1. Un Proceso Simplificado de una unidad de endulzamiento con Amina [9]

Figura 2. Esquemático para el reemplazo de una porción de la corriente de reflujo con agua fresca
Columna Contactora
- Corriente agria de gas es saturada con agua
- Número de platos teóricos = 7
- Diferencial de presión= 20 kPa (3 lpca)
- Temperatura de la corriente de amina pobre = temperatura del gas agrio de alimentación + 5.5 (10 )
Columna Regeneradora
- Numero de platos teóricos = 10 (excluyendo el condensador y rehervidor)
- Temperatura corriente rica = 98.9 (210 )
- Presión corriente rica = 414 kPag (60 lpcm)
- Temperatura del condensador = 48.9 (120 )
- Diferencial de presión = 28 kPag (4 lpc)
- Presión de fondo = 110 kPam (16 lpcm)
Carga Térmica Regeneradora = 132 kg vapor/m3 de solución de Amina (1.1 lbm/gallon) por gasto de circulación de amina.
Intercambiadores de Calor
- Diferencial de presión enfriador amina pobre = 35 kPa (5lpc)
- Presión costado rico = 35 kPa (5lpc)
- Presión costado pobre = 35 kPa (5lpc)
Bomba
- Presión descarga = Corriente alimentadora gas agrio + 35 kPa (5 lpc)
- Eficiencia = 65 %
Concentración y Gasto Amina Pobre
- Concentración MDEA en la solución pobre de amina/agua = 50 % por peso
- Gasto de la Amina pobre = 65.87 m3S/h (290 gpms)
(Esta circulación fue resultado de la carga total del gas sobre la amina rica de unos 0.40 moles gases ácidos/mol de amina)
Válvula de Expansión Solución Amina Rica
- Presión Tanque de despojo (flash tank) = 448 kPag (65 lpcm)
Resultados y Discusiones:
Basado en la descripción y especificaciones presentadas en la sección previa, ProMax [9] es usada para simular el diagrama de flujo del proceso de la Figura 1. Para cada corrida de simulación, las siguientes propiedades so reportadas:
- Concentración molar del metanol (PPM) en
- Gas dulce
- Gas de despojo del tanque
- Gas ácido del regenerador
- Concentración del metanol (%peso) en
- La amina rica
- Corriente de reflujo condensada (corriente 10)
- Corriente de reflujo recirculada (corriente 11)
- Concentración del H2S, y el CO2 en el gas dulce
Las concentraciones del H2S calculadas para el gas dulce fueron poco variadas por la concentración del reflujo de metanol. Los rangos fueron entre 3.92 hasta 3.61 PPMV y 1.64 hasta 1.81 PPM para temperaturas del gas agrio de 43.3 y 32.2°C (110 más 90°F), respectivamente. La presencia del metanol aumenta levemente el contenido del H2S en el gas dulce. La concentración calculada para el CO2 en el gas dulce fueron de 2.87 y 2.61 mol % para temperaturas de la alimentación agria de 43.3 y 32.2°C (110 y 90°F), respectivamente. De manera que, la presencia del metanol no imparte ningún efecto sobre el contenido del H2S y CO2 en el gas dulce.
La variación del contenido de metanol en el gas dulce como función del %molar de la corriente de reflujo purgada con agua fresca es presentada en las Figuras 3 al 5 para el gas dulce, gas de despojo, y gas ácido, respectivamente. En todas las figuras, la línea sólida y símbolos rellenos presentan 43.3°C (110°F) y las líneas punteadas y símbolos vacíos indican 32.2°C (90°F). Los símbolos cuadrados, círculos, y triángulos presentan un contenido de metanol en el gas ácido de 50, 250, y 500 PPMV, respectivamente.
La Figura 3 presenta la variación del contenido de metanol en el gas dulce en función de la reposición del reflujo con agua fresca para las dos temperaturas de la corriente agria de entrada y tres concentraciones de metanol (PPM) en ésta. Las dos temperaturas son 43.3 y 32.2 °C (110 y 90 °F). En las Figuras 3 al 8, PPM A, y PPM B representan 32.2 °C (110 y 90 °F), respectivamente.
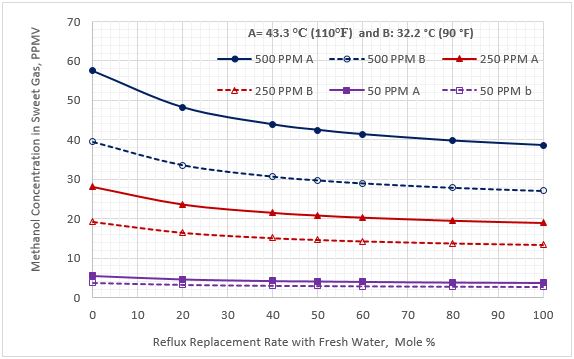
Figura 3. Contenido de metanol en la corriente de gas dulce vs el reemplazo del caudal de reflujo
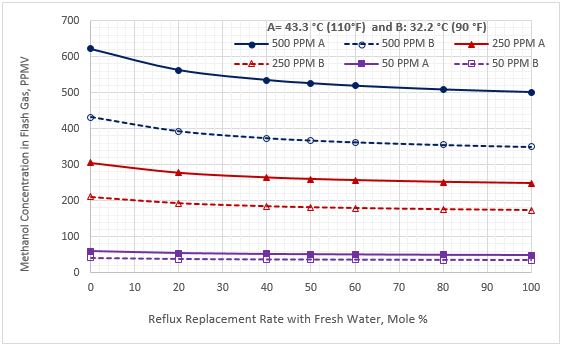
Figura 4. Contenido de metanol en la corriente de gas dulce vs el reemplazo del caudal de reflujo
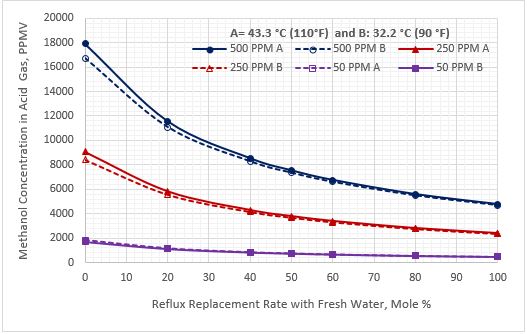
Figura 5. Contenido de metanol en la corriente de gas ácido vs el reemplazo del caudal de reflujo
La Figura 3 indica que mientras aumenta la purga de la corriente de reflujo de agua fresca, el contenido de metanol en el gas dulce disminuye. Para el caso de 100 % de purga, la reducción máxima de metanol es de un 33% para el caso de 43.3°C (110°F) y 500 PPMV y el mínimo es de un ~30% para el caso de 32.2°C (90°F) y 50 PPMV.
La Figura 4 presenta una tendencia similar para el contenido de metanol en la corriente del gas de despojo (flash gas). Para la condición de 100% de purga, la reducción máxima del metanol es de ~19.5% correspondiente con 43.3°C (110°F) y 500 PPMV y el mínimo es ~17.5% para el caso de 32.2°C (90°F) y 50 PPMV.
La Figura 5 presenta una tendencia algo distinta para el contenido de metanol en la corriente de gas. Esta figura indica que la corriente agria alimentadora no posee impacto discernible sobre el contenido de metanol en gas ácido. Para el caso de 100% de purga, la reducción del contenido de metanol fue observado en un rango de ~72 % hasta ~73% para todos los casos de las temperaturas y contenido de metanol de gas alimentador.
La variación del contenido de metanol como función del %molar de la corriente de reflujo reemplazada con agua fresca es presentada en las Figuras 6 al 8 para la amina pobre, reflujo purgado, y reflujo reemplazado, respectivamente.
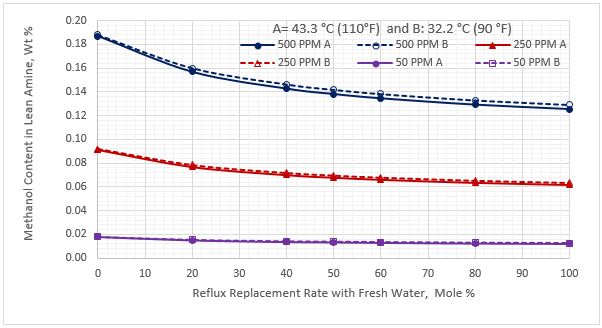
Figura 6. Contenido de Metanol en la corriente de amina pobre vs reemplazo del gasto de reflujo
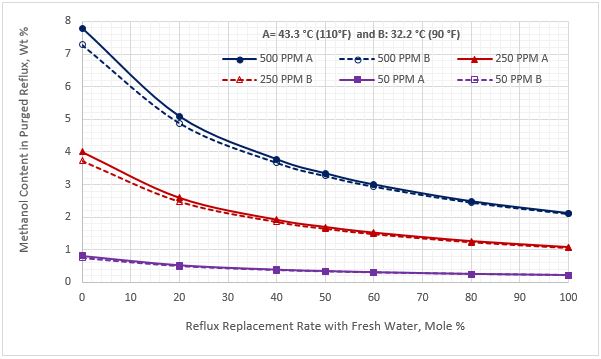
Figura 7. Contenido de Metanol en la corriente de purga de reflujo vs reemplazo del gasto de reflujo
La Figura 6 indica que mientras aumenta la purga de la corriente de reflujo con agua fresca, el contenido de metanol disminuye. Para una purga de 100%, la máxima reducción se ve en ~33% en el caso de 43.3°C (110°F) y 500 PPMV y el mínimo es de ~30% para el caso de 32.2°C (90°F) y 50 PPMV. Estos valores son los mismos a aquellos reportados para el contenido de metanol en el gas dulce. Esto es esperado por cuanto la corriente de amina pobre y gas dulce se contactan en equilibrio una con la otra.
La Figura 7 presenta tendencia similar para el contenido de metanol en la corriente de reflujo purgada. Para un 100% de purga, la reducción mínima de metanol es de ~71.2% coincidentes con 32.2°C (90°F) y 500 PPMV y un máximo de ~73.5% para el caso de 43.3°C (110°F) y 50 PPMV.
La Figura 8 presenta una tendencia distinta para el contenido de metanol en la corriente del gas ácido. Para un 100% de de purga, la reducción es de un 100 % para ambas temperaturas y los tres contenido del metanol en el gas de alimentación agrio.
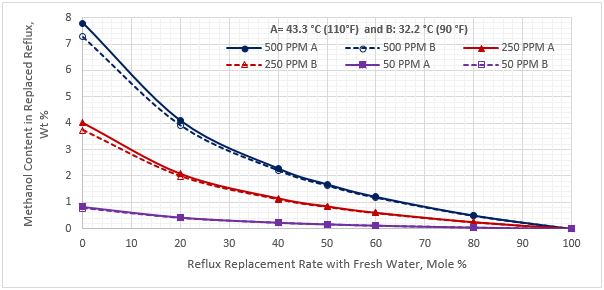
Figura 8. Contenido de Metanol en la corriente reemplazada de reflujo vs el gasto de reemplazo
Conclusiones:
Basado en los resultados obtenidos del caso en estudio, este PDM presenta las siguientes conclusions:
- El proceso de endulzamiento con MDEA remueve una cantidad considerable de metanol del gas agrio de alimentación. Adicionalmente, si el contenido de metanol en el gas agrio es alto, el gas dulce pudiése aun retener alto contenido de metanol, el cual podría causar inconvenientes en las operaciones de los procesos por emprenderse agua abajo.
- El mayor contenido de metanol debido al atrapamiento del mismo en el sistema se observa en la corriente de reflujo condensada 10
- Provisiones para la purga de reflujo (despojo de agua) y su reemplazo con “Agua Fresca” (Figuras 1 y 2) pueden mejorar la recuperación del metanol.
- El proceso básico de endulzamiento con MDEA redujo el contenido de metanol en el gas dulce por ~89% y ~92% en los casos de 43.3°C (110°F) y 32.2°C (90°F), respectivamente (Corriente 4 en la Figura 1).
- El proceso modificado de endulzamiento con MDEA con 100% de purga de la corriente de reflujo redujo el contenido de metanol en el gas dulce (PPMV) por ~92% y ~95% en los casos de 43.3°C (110°F) y 32.2°C (90°F), respectivamente. (Corriente 4 in Figura 1).
- La corriente de purga del reflujo, la cual contiene metanol debe ser eliminada adecuadamente o puede ser tratada dentro de la planta. El agua tratada a ser recuperada podría server como agua fresca en el proceso de endulzamiento.
El Metanol es tanto un Contaminante de Aire Dañino (HAP), así como un Compuesto Orgánico Volátil (VOC). Es regulado por el US EPA bajo premisas del Clean Air Act (Programa de Aire Puro) . De manera que los operadores deben asegurarse que su disposición es segura cuando se purga. Sin embargo, igual deben considerar su despojo a la atmósfera. Esto significa que de no haber la presencia de azufre, lo más probable es que el gas ácido no podrá ser arrojado (venteado) sin exceder los umbrales HAP/VOC. Debe ser enviado a un sistema de control, y aun más en este sitio, dependiendo de tamaño de la planta, el operador aun podrá entrar en el régimen de umbrales de control.
Para informarse adicionalmente sobre casos similares y como minimizar las instancias de problemas operacionales, le sugerimos su asistencia a nuestras sesiones técnicas designadas G6 (Gas Treating and Sulfur Recovery), G4 (Gas Conditioning and Processing), G5 (Advanced Applications in Gas Processing), y la PF4 (Oil Production and Processing Facilities)
PetroSkills / Campbell ofrece su experiencia en consultoría sobre este tema y muchos adicionales. Para mayor información sobre estos servicios, le invitamos su visita a nuestra dirección en la red al http://petroskills.com/consulting, o nos envían correo electrónico al consulting@PetroSkills.com.
By: Dr. Mahmood Moshfeghian
Traducido al Español por: Dr. Frank E. Ashford
References:
- Bullin, K.A., Bullin, J.A., “Optimizing methanol usage for hydrate inhibition in a gas gathering system,” Presented at the 83rd Annual GPA Convention – March 15, 2004.
- Szymczak, S., Sanders, K., Pakulski, M., Higgins, T.; “Chemical Compromise: A Thermodynamic and Low-Dose Hydrate-Inhibitor Solution for Hydrate Control in the Gulf of Mexico,” SPE Projects, Facilities & Construction, Dec, 2006.
- Gas Processors Association, “GPA RR-149: Vapor-Liquid and Vapor-Liquid-Liquid Methanol or Ethylene Glycol Solutions,” 1995. Equilibrium for H2S, CO2, Selected Light Hydrocarbons and a Gas Condensate in Aqueous
- O’Brien, D., Mejorada, J., Addington, L., “Adjusting Gas Treatment Strategies to Resolve Methanol Issues,” Proceedings of Lawrence Reid Gas Conditioning Conference, Norman, Oklahoma, 2016.
- Moshfeghian, M., October 2010 tip of the month, PetroSkills – John M. Campbell, 2010.
- Moshfeghian, M., July 2014 tip of the month, PetroSkills – John M. Campbell, 2014
- Maddox, R.N., and Morgan, D.J., Gas Conditioning and Processing, Volume 4: Gas treating and sulfur Recovery, Campbell Petroleum Series, Norman, Oklahoma, 1998.
- Campbell, J.M., Gas Conditioning and Processing, Volume 2: The Equipment Modules, 9th Edition, 1st Printing, Editors Hubbard, R. and Snow –McGregor, K., Campbell Petroleum Series, Norman, Oklahoma, 2014.
- ProMax 4.0, Bryan Research and Engineering, Inc., Bryan, Texas, 2016.
No comments yet. You should be kind and add one!
By submitting a comment you grant Campbell Tip of the Month – Spanish a perpetual license to reproduce your words and name/web site in attribution. Inappropriate and irrelevant comments will be removed at an admin’s discretion. Your email is used for verification purposes only, it will never be shared.