Existen distintas configuraciones de proceso para la deshidratación por adsorción. Los arreglos más comunes son de dos y tres contactores. Uno puede informarse sobre éstos y la descripción de los procesos en el Capítulo 18 del Texto de la John M. Campbell [1]. Las Figuras 1, y 2 presentan un diagrama de flujo de proceso simplificado para los citados sistemas de dos, y tres contactores, respectivamente. Estas unidades pueden reducir el contenido de agua de una corriente de gas a menos de 0.1 ppmv. La Industria del Gas normalmente aplica los sistemas de deshidratación por adsorción aguas arriba al proceso de licuefacción en una Planta de Gas Natural Licuado (GNL) en donde la temperatura se reduce a menos de -160 °C (-256 °F) y -100 °C (-148 °F), respectivamente. Remoción del vapor de agua del gas a estos valores mínimos es esencial para evitar un escenario de congelamiento.
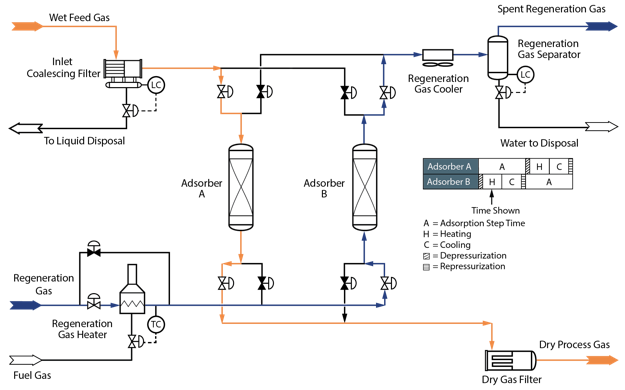
Figura 1. Un Diagrama de Flujo de Proceso para un Sistema de Deshidratación por Adsorción de Dos Torres
En un Sistema de dos – torres, mientras las Torre A se encuentra en proceso de adsorción, la Torre B se ve en regeneración. Posterior al ciclo de adsorción por la Unidad A, ésta es cambiada al modo de regeneración y la Torre B inicia su proceso de Adsorción. A cualquier momento una de las Torres se ve adsorbiendo el vapor de agua mientras que la otra está en proceso de regeneración.
En la configuración de Tres Torres, a cualquier tiempo, dos torres (e.i. A y B) operan mediante el proceso de adsorción en paralelo escalonado, mientras que la tercera torre (e.i C) ésta en regeneración. En esta configuración, la mitad del gas de proceso es admitida a la Torre A, y el resto se admite por la Torre B, como se observa en el gráfico de operación insertado en la Figura 2.
![Figura 2. Un diagrama de Flujo de Proceso para un Sistema de adsorción por tres – torres [1].](http://www.jmcampbell.com/tip-of-the-month/spanish/wp-content/uploads/2016/02/fig2-1.png)
Figura 2. Un diagrama de Flujo de Proceso para un Sistema de adsorción por tres – torres [1].
Este previo del mes (PDM) compara las dimensiones requeridas para el equipo mayor relacionado con Unidades de Dos y Tres Torres. Esta compracación considera los siguientes parametros.
- Masa del Adsorbente
- Diametro del Lecho
- Altura del Lecho
- Gasto del Gas de Regeneración
- Carga Térmica de Calentamiento del Gas de Regeneración
- Carga Térmica de Enfriamiento del Gas de Regeneración
- Carga Térmica de Regeneración del Gas
- Espesor de la Chapa del Contactor y la masa.
La Tabla 1 presenta la descripción de éstas dos configuraciones.
Tabla 1. Configuración de las Torres (Contactores)
Esta discusión asume un gasto de gas de alimentación de 2.83×106 m3S/d (100 MMPCSD) con torres externamente aisladas. Examina dos condiciones de alimentación de:
- 30°C (86°F) y 6.207 MPaa (900 lpca)
- Contenido estimado de agua de = 699 kg/106 m3S (43.7 lbm/MMPCS)
- Carga de agua por torre de 2-Torres por hora = 4 kg/h (182 lbm/hr)
- Carga de agua por Torre por ciclo = 989 kg (2185 lbm)
- Carga de agua por torre para 3-Torres por hora = 2 kg/h (91 lbm/hr)
- Carga de agua por Torre por ciclo = 662 kg (1456 lbm)
- Carga de agua por torre de 2-Torres por hora = 4 kg/h (182 lbm/hr)
- Contenido estimado de agua de = 699 kg/106 m3S (43.7 lbm/MMPCS)
- 40°C (104°F) y 8.0 MPaa (1160 lpca)
- Contenido estimado de agua de = 974 kg/106 Sm3 (61 lbm/MMPCS)
- Carga de agua por torre de 2-Torres por hora = 115 kg/h (254 lbm/hr)
- Carga de agua por Torre por ciclo = 1378 kg (3050 lbm)
- Carga de agua por torre para 3-Torres por hora = 5 kg/h (127 lbm/hr)
- Carga de agua por Torre por ciclo = 920 kg (2033 lbm)
- Carga de agua por torre de 2-Torres por hora = 115 kg/h (254 lbm/hr)
- Contenido estimado de agua de = 974 kg/106 Sm3 (61 lbm/MMPCS)
Los remanentes parámetros especificados son:
- Adsorbente = Tamiz Molecular Tipo 4A, 3.2 mm (1/8 pul) diametro
- Carga de Equilibrio del Adsorbente, ΔXnew = 19 peso% (masa de agua/100 masa de adsorbente)
- Factor de Vida del Adsorbente FL = 0.6 (Basado en 3 años y rendimiento promedio)
- Densidad del Adsorbente = 705 kg/m3 (44 lbm/pie3)
- Capcidad de Calor del Adsorbente = 1.0 kJ/kg-°C (0.24 Btu/lbm-°F)
- Capacidad de Calor de la Chapa = 0.5 kJ/kg-°C (0.12 Btu/lbm-°F)
- Densidad Relativa del Gas de Alimentación = 0.7
- Densidad Relativa del Gas Seco de Regeneración = 0.59
- Presión del Gas de Regeneración = 2.07 MPaa (300 lpca)
- Temperatura del gas de Regeneración al Calentador = Temperatura gas Entrada
- Temperatura del Gas del Calentador = 288 °C (550 °F)
- Temperatura de reposo del lecho antes del enfriamiento = 260 °C (500 °F).
Resultados de los Cómputos
Basado en el procedimiento más los paso del Capítulo 18 [1], este PDM utiliza la versión actualizada del “Conjunto Electrónico de Cómputos” (Software) de la PetroSkills/Campbell, GCAP para lograr los resultados de todos los cómputos.
La Figura 3A indica la variación de la masa requerida del adsorbente por torre con el contenido de agua del gas de entrada para las configuraciones de dos y tres torres. Mientras la carga de agua aumenta, le masa requerida aumenta fijando el tiempo de adsorción. Nótese que ésta carga de agua de entrada aumenta con el aumento de temperatura pero disminuye con un aumento en la presión. La carga de agua por torre es función de éste contenido de agua de alimentación, tiempo de adsorción, y gasto del gas existente en la torre.
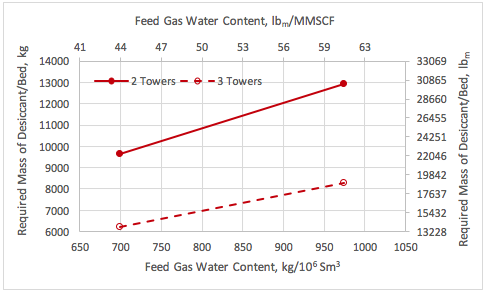
Figura 3A. Masa del adsorbente por torre vs el contenido de agua de entrada y numero de torres.
Para obtener esencialmente la misma masa total adsorbida en las dos configuraciones, se aplicó la siguiente relación:
θA = 0.75 θB
Donde θA es el tiempo de adsorción por torre para una sistema de dos-contactores y θB es el tiempo total para un sistema de tres – contactores. Ésta relación es obtenida de:
(Caudal Total)(θA)(2 Torres) = (1/2 Caudal Total) (θB)(3 Torres)
La masa total requerida por las configuraciones de dos-torres y las de tres son distintas por cuanto la longitud de la zona de transferencia de masa de la unidad de tres torres es menor que la de dos. Por cuanto el adsorbente es vendido en incrementos de 300 lbm (136.1 kg), la mas de cada torre fue “redondeada” hacia la próxima unidad de 300 lbm (136.1 kg). La masa total calculada de los adsorbentes de la configuración de dos – torres son de 19323 y 25855 kg (42600 y 57000 lbm) para la alimentación de menor y mayor contenido de agua respectivamente. Las masas correspondientes de la unidad de tres – torres son de 18779 y 25719 kg (41400 y 56700 lbm). Similarmente, la Figura 3B presenta la masa requerida del hierro por torre como función del contenido de vapor de agua en el gas de alimentación y numero de torres.
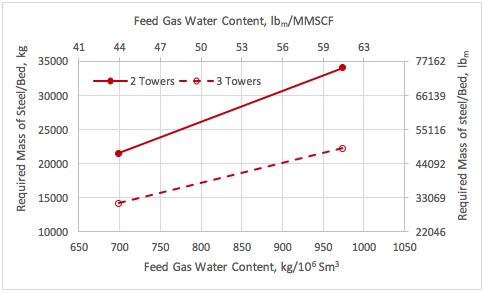
Figure 3B. Masa de hierro por torre vs el contenido de agua del gas de entrada y numero de torres.
La masa del adsorbente en la torre y criterio de caída de presión establecen el diámetro de ésta y altura del lecho. Éste cómputo es uno de ensayo y error. La Figura 4 indica la variación del diámetro de la unidad con el contenido de agua del gas de entrada, y numero de torres.
Como el caudal del gas por torre de un sistema de dos – torres es el doble del caudal del sistema de tres, el diámetro de los contactores de dos torres debe ser mayor que el de tres para cumplir con la caída de presión permisible de menos de 41 kPa (6 lpc). La Figura 4 indica que el factor limitante es la caída de presión y el contenido de agua de entrada posee mínimo impacto sobre el diámetro del lecho. La velocidad superficial del gas para todos los casos mostró variación entre 0.10 – 0.15 m/s (20 – 30 pie/min).
Después de determinar el diámetro del lecho (torre), es posible calcular la altura del lecho conociendo la masa del mismo, diámetro de la torre, y la densidad del adsorbente. De la Figura 5 se observa la variación de la altura mínima del adsorbente con contenido de agua de entrada y numero de torres. Esta figura indica que con mayores contenidos de carga de agua la altura del lecho aumenta, mientras que menores cargas de agua requieren menor altura de lecho. Como el diámetro de un sistema de dos torres es el mayor, su altura es menor.
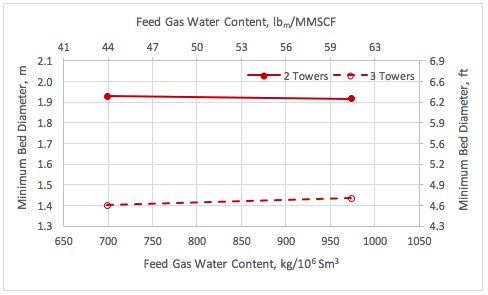
Figura 4. Diámetro del Lecho vs contenido de agua del gas de entrada y número de torres
La Figura 6 indica la variación del gas de regeneración con contenido de agua del gas de alimentación asumiendo tiempos constantes para el calentamiento y enfriamiento. Esta figura muestra que para mayores cargas de vapor de agua de entrada se requiere mayor gas de regeneración. Sin embargo, el gas de regeneración es prácticamente el mismo para las dos configuraciones en consideración.
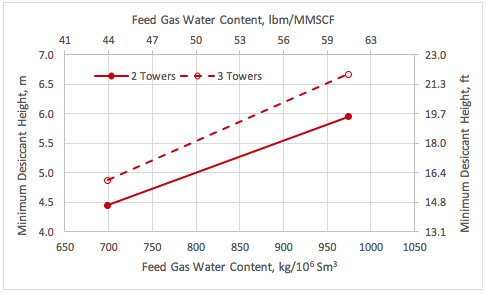
Figura 5. Altura de lecho vs contenido de agua en el gas de entrada y numero de torres.
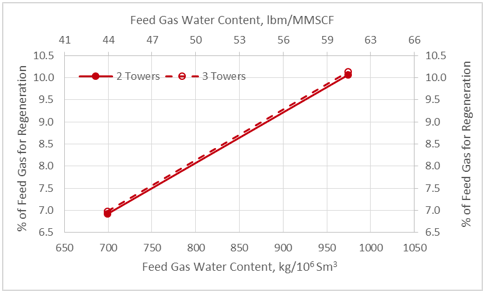
Figura 6. Porcentaje % del gas de entrada para la regeneración vs contenido de agua en el gas de entrada y numero de torres.
De manera similar, las Figuras 7,8, y 9 indican las variaciones de las cargas térmicas de calentamiento más enfriamiento, y en adición la del gas de regeneración en función de la carga de agua del gas de entrada y el número de torres. Como las torres de un sistema de dos son de mayor diámetro que las de un sistema de tres, las cargas térmicas tanto de calentamiento como enfriamiento son mayores que las de un sistema de tres torres (figuras 7, y 8). Sin embargo, la Figura 9 muestra que los requerimientos de calor para el gas de regeneración son casi iguales para las dos configuraciones.
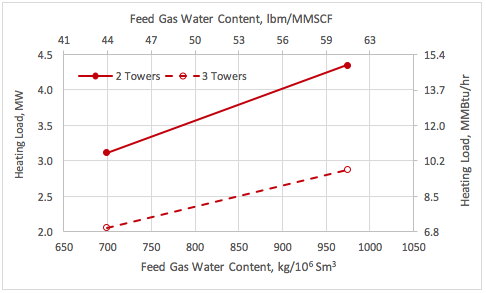
Figura 7. Carga térmica de calentamiento vs contenido de agua y número de torres.
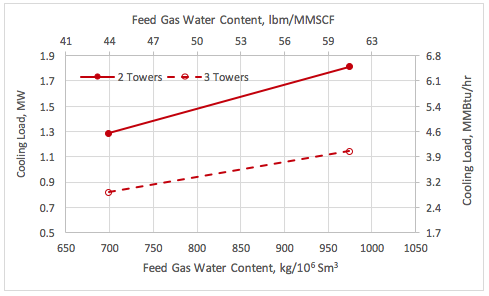
Figura 8. Carga térmica de enfriamiento vs contenido de agua y número de torres.
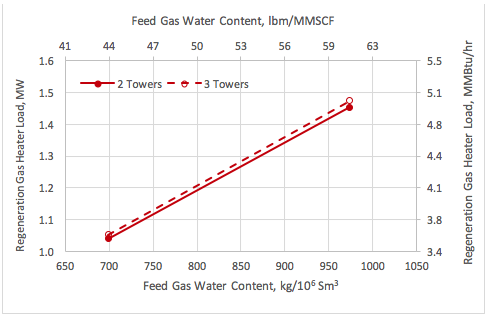
Figura 9. Carga térmica de para el gas de regeneración vs contenido de agua y número de torres .
Resumen:
El contenido de agua en un gas de alimentación afectado por le temperatura, presión y caudal del gas es el parámetros clave en el dimensionamiento de un sistema de deshidratación por adsorción. Mayores contenidos de agua requieren un lecho de mayor masa, mayores cargas térmicas de calentamiento y enfriamiento, y mayores gastos del gas de regeneración.
En los casos evaluados en este Previo del Mes (PDM), los diámetros en los sistemas de dos – torres son mayores que los de tres, pero su longitud es menor. La masa del adsorbente y masa del hierro (chapa) por torre en el sistema de dos – torres son mayores que los de tres. De manera que, las cargas térmicas de calentamiento y enfriamiento son mayores en el sistema de tres – torres. Las cargas térmicas para el gas de regeneración son casi las mismas para ambos escenarios.
Para informarse adicionalmente sobre casos similares y como minimizer sus problemas operacionales, les invitamos asistir a nuestras sesiones técnicas PF49 (Troubleshooting Oil and Gas Facilities), PF42 (Separation Equipment Selection and Sizing), G4 (Gas Conditioning and Processing), G5 (Gas Conditioning and Processing – Special), y PF4 (Oil Production and Processing Facilities),
PetroSkills ofrece su experiencia en la consultoría sobre este tema y muchos adicionales. Para mayor información, les invitamos nos visiten en nuestra dirección en la red al http://petroskills.com/consulting, o nos envían correo electrónico al consulting@PetroSkills.com.
Dr. Mahmood Moshfeghian
Traducido al Español por : Dr. Frank E. Ashford
References:
- Campbell, J.M., Gas Conditioning and Processing, Volume 2: The Equipment Modules, 9th Edition, 2nd Printing, Editors Hubbard, R. and Snow–McGregor, K., Campbell Petroleum Series, Norman, Oklahoma, 2014.
- Malino, H. M., http://www.jmcampbell.com/tip-of-the-month/2015/05/benefits-of-standby-time-in-adsorption-dehydration-process/
- Moshfeghian, M., http://www.jmcampbell.com/tip-of-the-month/2015/10/what-is-the-impact-of-feed-gas-conditions-on-the-adsorption-dehydration-system/
- GCAP Version 9.1.1, Gas Conditioning and Processing Software, Editor Moshfeghian, M., PetroSkills/Campbell, Norman, Oklahoma, 2015.
No comments yet. You should be kind and add one!
By submitting a comment you grant Campbell Tip of the Month – Spanish a perpetual license to reproduce your words and name/web site in attribution. Inappropriate and irrelevant comments will be removed at an admin’s discretion. Your email is used for verification purposes only, it will never be shared.